Cerakote
Finishing / Post Processing for 3D Printed Parts
Cerakote is a thin-film ceramic coating which improves part performance and aesthetics. This industry-leading coating is extremely durable and is scratch resistant, chemical resistant, heat resistant, liquid resistant and UV resistant. When applied Cerakote is approximately 0.002" thick.
Cerakote is popular in a variety of industries including automotive, aerospace, electronics, medical devices, consumer products and defense. Companies that rely on Cerakote coatings include Boeing, SpaceX, Blue Origin, Ford, Lamborghini, as well as the US Department of Defense.
Cerakote is compatible with a wide variety of metals and plastics, has been tested and verified for Nylon 3D printed with HP Multi Jet Fusion.
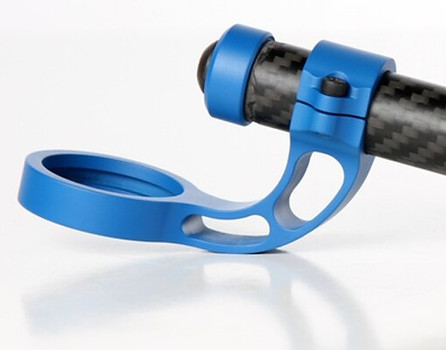
About Cerakote
Benefits
-
Hydrophobic. Cerakote repels water and prevents water absorption.
-
Scratch resistant. Cerakote adds scratch resistance to plastics to help minimize wear over time. If scratched, the adjacent coating remains in place.
-
Resistant to chemicals. Cerakote is resistant to to acids and solvents, including acetone and diesel.
-
Durable. Cerakote modifies the surface of the polymer to a harder and more durable finish.
-
UV resistant. Cerakote protects materiasl from UV damage, extending the life of products exposed to sunlight and harsh outdoor conditions.
-
Thermal barrier properties. Cerakote protects surfaces from high heat exposure.
Design Considerations
Cerakote is applied while the parts are hung in commercial racks so the hanging of the parts may leave a cosmetic blemish. When ordering it is advisable to identify customer-facing surfaces or add hanging loops to the design.
Testing and Certifications
Cerakote ASTM testing on HP Nylon PA12
Tests were performed by the Cerakote Technical Training Team on 3D printed parts manufactured by HP with with Multi Jet Fusion technology.
ASTM Test results on Graphite Black (H-146)
-
Cross Hatch Adhesion
-
ASTM D3359 method A: 5A
-
ASTM D3359 method B: 4B
-
ASTM D3363 scratch / gouge: 9H / 7H
-
-
ASTM D4752 - 24 hour Submersion
-
Water
-
before and after mass: + 0.03 grams
-
visual color change: no discoloration
-
-
Acetone
-
before and after mass: + 0.07 grams
-
visual color change: no discoloration
-
-
Diesel
-
before and after mass: + 0.07 grams
-
visual color change: no discoloration
-
-
-
ASTM D1729 - Color Deviation
-
L/A/B Color L: 0.4 / A: 0.009 / B: 0.06
-
Deviation of mass across 16 samples: mass 0.42 grams
-
-
ASTM D523 - Gloss Deviation
-
Gloss standard deviation at 60 degrees: 0.14
-
Test results on Stormtrooper White (H-297)
-
Cross Hatch Adhesion
-
ASTM D3359 method A: 4A
-
ASTM D3359 method B: 4B
-
ASTM D3363 scratch / gouge: 9H / 6H
-
-
ASTM D4752 - 24 hour Submersion
-
Water
-
before and after mass: + 0.02 grams
-
visual color change: no discoloration
-
-
Acetone
-
before and after mass: + 0.11 grams
-
visual color change: no discoloration
-
-
Diesel
-
before and after mass: + 0.02 grams
-
visual color change: no discoloration
-
-
-
ASTM D1729 - Color Deviation
-
L/A/B Color L: 0.18 / A: 0.03 / B: 0.13
-
Deviation of mass across 16 samples: mass 0.42 grams
-
-
ASTM D523 - Gloss Deviation
-
Gloss standard deviation at 60 degrees: 0.65
-
Cerakote ASTM Wear and Abrasion Tests
Taber Abrasion Test (ASTM D4060)
Seven competitive finishes including Cerakote H-146 Graphite Black were tested in accordance with ASTM D4060. Each finish was tested three separate times in order to validate the test result.
In this test, Cerakote lasted nearly twice as long as the nearest competitive finish and 24 times as long as the furthest competitive finish.
Impact Resistance Test (ASTM D2794)
A 12-gauge shotgun was used to test the flexibility of Cerkote, with impresssive results.
All Cerakote Elite and nearly every Cerakote H Series have an impact strength measuring 160 in-lbs., which is the maximum the impact tester can measure. The Impact Resistance test (ASTM D2794) measures the resistance of organic coatings to the effects of rapid deformation (Impact).
Available Colors
NRA Blue (H-171P)
Gloss: Flat Gloss units: 4
Corvette Yellow (H-144)
Gloss Gloss units: 73
Matte Armor Clear (H-301)
Semi Gloss Gloss units: 58
Firehouse Red (H-216P)
Gloss: Matte Gloss units: 9
Gloss Black (H-109)
Semi Gloss Gloss units: 51
Bright White (H-140P)
Semi Gloss Gloss units: 49
Graphite Black (H-146)
Matte Gloss units: 9
Don't see what you are looking for? Contact us to discuss options.