Case Study - Creating Replacement Parts for Marine Applications with 3D Scanning and 3D Printing
A boat owner in Trail BC broke a critical part in the throttle mechanism in his boat and was unable to source an affordable replacement. The owner was able to improve the part design and manufacture a replacement quickly and affordably, with the help of Tempus 3D's 3D scanning and additive manufacturing technology.
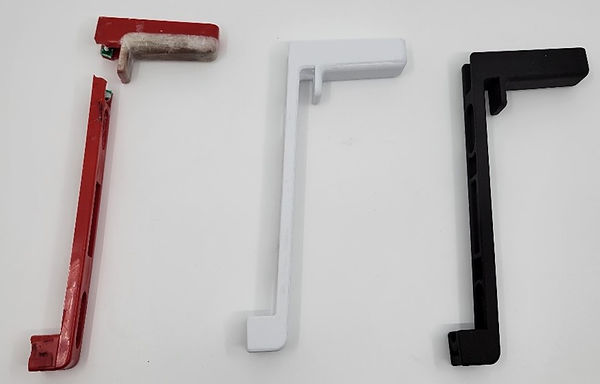
Key Benefits
-
Reduce cost of replacement parts.
-
Create replacements when parts are unavailable.
-
Opportunity to improve design and performance to eliminate future failures.
-
Reduce environmental impact by replacing parts instead of discarding assemblies.
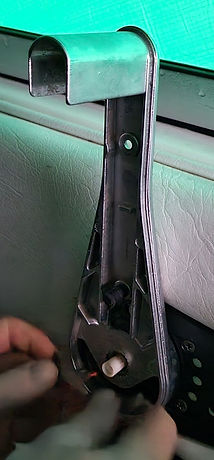
Industry
Marine, replacement parts, consumer goods
Partners
Selkirk Technology Access Centre
Selkirk College Digital Fabrication & Design
Material
Software
Fusion 360
Post Processing
Black dye
Introduction
Paul was heading out for a day on the lake with his family when a critical component in his boat failed, forcing him to bring the boat back to shore and cancel his plans. The failure happened in the throttle assembly as he was heading out for a day on the water. The plastic trigger that engages the throttle had snapped, leaving Paul unable to operate the boat. The boat was limped to shore where it was loaded onto the boat trailer and hauled back to town.
Challenge
The boat was taken to a local marine repair shop for diagnostics. It was quickly determined that the failure was due to the broken piece of red plastic located within the throttle control housing, as shown in the picture. The marine repair shop informed Paul that the piece was not available for purchase individually and he would have to purchase an entire throttle assembly. This seemed unnecessarily expensive and wasteful, so Paul decided to seek other solutions.

Paul's first thought was to superglue the broken pieces back together. This was the simplest solution, but he knew this was a temporary fix and the part would break again under similar circumstances. When the part originally broke Paul was fortunate to be close to shore, but the last thing he wanted was for the part to break again in an isolated area. He decided that superglue was not an acceptable solution and began to explore other options.
As he considered his options, Paul realized that a friend of his had a son who may be able to help him out. The individual was employed as a summer student at the Selkirk Technology Access Center and had experience with CAD modelling and 3D printing. Paul reached out to the student and brought him the broken part, only to be told that the part was too complex to be easily designed without a great deal of time and effort. He was also told that not all 3D printing processes or materials would be suitable for building a replacement part, as many 3D printing processes are weak between the printing layers.
Solution
It seemed as though Paul would have to buy a new assembly after all, which would be costly and require a lot of installation work. But as luck would have it the summer student consulted with the Digital Fabrication and Design department within Selkirk College, who proposed an alternate solution. The student was able to use 3D scanning technology to create a digital CAD file of the broken part. The CAD file was then used to reverse-engineer the part to fit the original housing. The design was also improved by increasing the material thickness where original part failed.
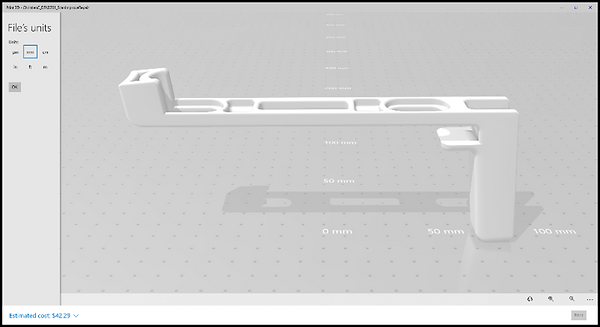
To test the design, a prototype was created with PLA plastic on a consumer-grade FDM printer. The prototype was used to test the fit and function of the part before final production.
Once the prototype was tested and approved, the design was brought to Tempus 3D to be manufactured with a material robust enough to withstand abuse and prolonged exposure to the elements. The team at Tempus recommended building the final part with Nylon 12, using HP Multi Jet Fusion (MJF) 3D printing technology. Nylon 12 is a robust production-grade plastic which is resistant to moisture, chemicals and UV light, suutabel for use in marine applications and outdoor environments. MJF technology is designed for commercial production of affordable end-use parts, and the unique printing process provides the density and strength needed for long-term use. This technology is used by major manufacturers such as Volkswagen, BMW and Ford, making it a logical choice for this application.
Result
The combination of an upgraded part design, robust material and a commercial manufacturing process resulted in a part much stronger than the original, which was made with injection-moulded plastic. Paul was able to save time and money while improving the part design and minimizing unnecessary waste.
About Tempus 3D
With industry-leading technology and a network of production partners, Tempus 3D is uniquely capable of serving innovators and manufacturers across Canada. With online ordering, the ability to turn around rush orders in as little as 36 hours and cost-effective overnight shipping we can ensure you have the parts you need on-time and on-spec. We at Tempus feel this is just the beginning of what manufacturing will look like in the future; it will be more responsive, more custom, and more local allowing innovators across sectors to bring products to market quicker and in a more environmentally friendly way.

Explore the possibilities of 3D scanning and reverse engineering
Learn more about manufacturing solutions with Tempus 3D
Explore industrial plastics available through Tempus 3D
Learn more about the advantages of industrial 3D printing with HP Multi Jet Fusion technology
Learn more about designing for 3D printing