Quiet Power: How Tempus 3D Helped Push the Limits of Drone Propulsion
- jonathang22
- 2 days ago
- 2 min read
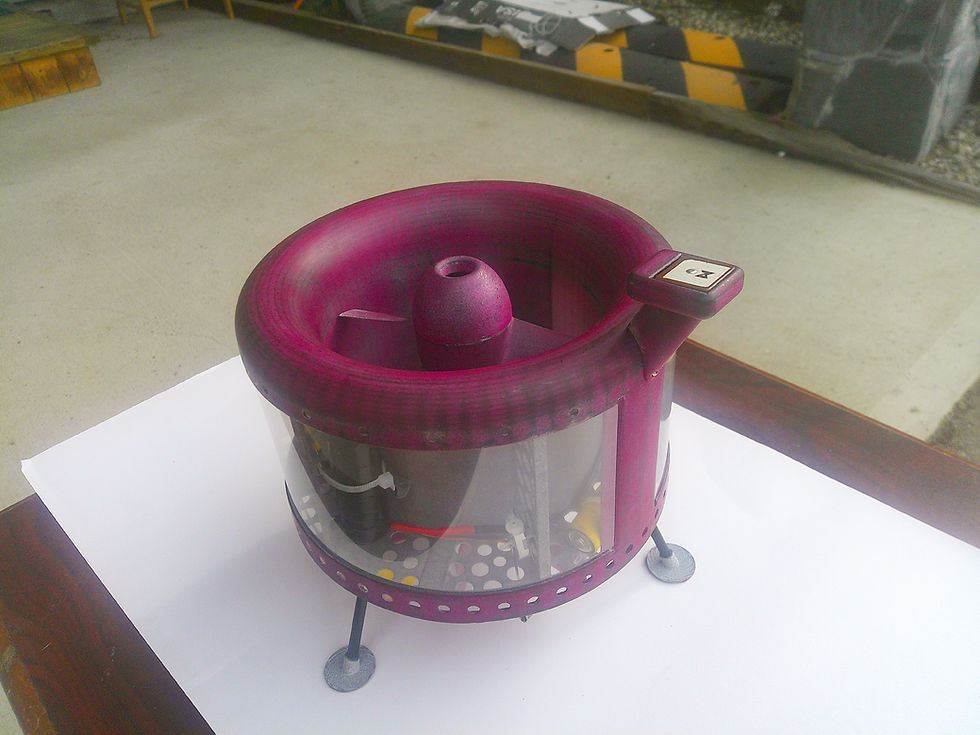
When Philip started building aircraft as a teenager, he wasn’t just exploring how things fly—he was questioning how they should. Years later, he’s become a specialist in a complex area of drone design: ducted, counter-rotating propulsion systems that emphasize safety, reduced noise, and control.
“My drones aren’t flying cameras,” Philip says. “They’re platforms for testing new propulsion concepts.”
With experience contributing to open-source tools like MIT’s Xrotor and the FTC suite, Philip builds drones from the ground up. His goal is to develop compact, quiet UAVs that are safer to operate near people—and more efficient than traditional open-rotor designs.Achieving that means working within tight design constraints.
“We’re running at 14,000 RPM with 0.7 mm tolerances,” he explains. “You can’t prototype that with off-the-shelf parts. The material and accuracy have to be reliable.”
That’s where Tempus 3D came in.

Using HP’s Multi Jet Fusion 5200 system, Tempus helped Philip prototype complex components—fan ducts, housings, and control structures—with the precision and durability needed for high-performance testing.
“Tempus made it possible to move quickly without compromising on quality,” he says. “I’m not building for show—I’m building to solve real engineering problems. That means fast iteration, aggressive testing, and confidence in the parts I’m using.”
Philip also designed a custom 2-axis gimbal rig and thrust bench to measure performance in real-world conditions, allowing him to refine each iteration without risking a full flight test.
His advice to others working in UAV development? Skip the templates.

“There are enough cookie-cutter quadcopters out there. If you’re going to build something, make it count. Innovate.”
At Tempus 3D, we’re proud to support that kind of work—engineering that moves the field forward, one well-built part at a time.